Help Needed Apply Within...
Help Needed Apply Within...
Hi guys,
Im after a favour... im doing some panel work on the safari and its doing my head in.
Im not sure what im doing wrong or if its the welder or what... so are any of you guys on here panel beaters/sheet metal workers/ just know what your doing??
I would like someone to cast an eye over it/help me get it done...
Am happy to pay for refreshments or fuel of choice...
Im up in Warkworth though so Id say my audience is limited...
Cheers
Caleb
0276834327
Im after a favour... im doing some panel work on the safari and its doing my head in.
Im not sure what im doing wrong or if its the welder or what... so are any of you guys on here panel beaters/sheet metal workers/ just know what your doing??
I would like someone to cast an eye over it/help me get it done...
Am happy to pay for refreshments or fuel of choice...
Im up in Warkworth though so Id say my audience is limited...
Cheers
Caleb
0276834327

027 MUD GEAR - (027 683 4327)
Check our facebook:
http://www.facebook.com/Filthy4x4
http://www.facebook.com/Filthymotorsportnz
- mudlva
- Hard Yaka
- Posts: 2918
- Joined: Mon Apr 16, 2007 12:00 pm
- Location: fixing another cv!! dam lockers (Papakura)
Re: Help Needed Apply Within...
ok explain what you are doing
dont bother to say whether its right or wrong just just your total process
i will give a few starters
size or amp of mig unit
size of wire and type
amp settings
what gas
is the existing steel been cleaned right back to bear steel surface
is the donner steel clean and shinny
what are you actually trying to do?
chassis/bar mods
guard chop
rust repair
what is the results of your welding looking like
are you blowing holes
is the weld pooling on top but the substrate breaks away quite easy under the weld itself
alot of welding is by trial and error if you are doing guard work see if you can find a old panel kicking around cut it into usable pieces and start welding it back together, butt welds, over lap welds, right angles, tapping pieces.
also start hot and turn it down to get to a stage where the holes only appear sometimes this will be better then a cold weld which looks good but has no penetration and falls apart easy
right o your turn
dont bother to say whether its right or wrong just just your total process
i will give a few starters
size or amp of mig unit
size of wire and type
amp settings
what gas
is the existing steel been cleaned right back to bear steel surface
is the donner steel clean and shinny
what are you actually trying to do?
chassis/bar mods
guard chop
rust repair
what is the results of your welding looking like
are you blowing holes
is the weld pooling on top but the substrate breaks away quite easy under the weld itself
alot of welding is by trial and error if you are doing guard work see if you can find a old panel kicking around cut it into usable pieces and start welding it back together, butt welds, over lap welds, right angles, tapping pieces.
also start hot and turn it down to get to a stage where the holes only appear sometimes this will be better then a cold weld which looks good but has no penetration and falls apart easy
right o your turn
Re: Help Needed Apply Within...
Apologies, I should have put up more info but was on my phone.
Its a 190amp Single phase on gas (Argoshield), have tried both 0.6 and 0.8 wire and tips.
Im attempting to weld the roof up on the safari, chopped the body.
Ive welded it 3 times
and when I grind it back (have used both grinder and flap disk) it looks ok(ish) when welded but when I grind it back it looks like it has severe under cutting/ weld pooling on top and it looks like it would break off very easy.
Ive never done panel steel before and didnt realize how hard it actually is
Ive tried all sorts of different settings, amps, volts, wire speed, gas reg. adjustments. Try it on an offcut and it goes wicked then do it on the truck and sometimes its perfect then all of a sudden it will cough splutter and blow holes etc...
Steel has been taken back too bare via flap disk, I am also welding outdoors with a small wind barrier.
Hopefully thats enough info, im really not sure if its the welder or me but I am blaming operator error for now
Cheers
Its a 190amp Single phase on gas (Argoshield), have tried both 0.6 and 0.8 wire and tips.
Im attempting to weld the roof up on the safari, chopped the body.
Ive welded it 3 times


Ive never done panel steel before and didnt realize how hard it actually is


Ive tried all sorts of different settings, amps, volts, wire speed, gas reg. adjustments. Try it on an offcut and it goes wicked then do it on the truck and sometimes its perfect then all of a sudden it will cough splutter and blow holes etc...
Steel has been taken back too bare via flap disk, I am also welding outdoors with a small wind barrier.
Hopefully thats enough info, im really not sure if its the welder or me but I am blaming operator error for now

Cheers

027 MUD GEAR - (027 683 4327)
Check our facebook:
http://www.facebook.com/Filthy4x4
http://www.facebook.com/Filthymotorsportnz
Re: Help Needed Apply Within...
I was blowing holes with mine (inside - 140 amps 8mm wire and co2 gas).
I found to get the penetration I used a piece of copper (ali will do as well) to draw heat from the area (hold it behind the panel joint) and I got better welds.
Of course I could be way off. I found practice with offcuts and some time tinkering with settings.
You tube is good for observing techniques but practice is best. Sorry there is no simple answer.
Heath
I found to get the penetration I used a piece of copper (ali will do as well) to draw heat from the area (hold it behind the panel joint) and I got better welds.
Of course I could be way off. I found practice with offcuts and some time tinkering with settings.
You tube is good for observing techniques but practice is best. Sorry there is no simple answer.
Heath
Re: Help Needed Apply Within...
Thanks Heath, I might see if I can find something to use, not sure where I would find anything like that where I am.
Will just have to keep trying, I just dont want to stuff it completely

Will just have to keep trying, I just dont want to stuff it completely



027 MUD GEAR - (027 683 4327)
Check our facebook:
http://www.facebook.com/Filthy4x4
http://www.facebook.com/Filthymotorsportnz
- waza4x4toy
- Bush Crasher
- Posts: 69
- Joined: Sat Jun 09, 2012 9:54 pm
- Location: North Shore
Re: Help Needed Apply Within...
Hi should try welding a jeep the panel steel is not like the cans your jappa is made of Caleb may be that's the problem
check out this nz you tuber he has about a dozen great panel and welding clips
See this one on welding panel [url]http://m.youtube.com/watch?v=zdsOGDzuIps&desktop_uri=%2Fwatch%3Fv%3DzdsOGDzuIps/url]
Very helpful and useful tips and tricks on most panel work.... his youtube ID is "restolad" if the above link is not working
Cheers W



check out this nz you tuber he has about a dozen great panel and welding clips
See this one on welding panel [url]http://m.youtube.com/watch?v=zdsOGDzuIps&desktop_uri=%2Fwatch%3Fv%3DzdsOGDzuIps/url]
Very helpful and useful tips and tricks on most panel work.... his youtube ID is "restolad" if the above link is not working
Cheers W
- mudlva
- Hard Yaka
- Posts: 2918
- Joined: Mon Apr 16, 2007 12:00 pm
- Location: fixing another cv!! dam lockers (Papakura)
Re: Help Needed Apply Within...
just thought of something
whats your helmet like if its set to dark then you will be having issues of not seeing the heat properly.
but
dont have it set to light either as arc eye is a bitch
also try spot migging on the panel steel, with a slighty hotter setting, start on the weld and pull the pool across onto the sheet, then off and start again starting back on the weld just done, ive found that this works quite well and im using 1.0 wire onto LC panels which would be 1.0-1.2 at a guess
i would be using around 25%-30% on a 250amp unit and getting reasonably flat welds with full penetration.
the donner steel is mainly 1.6mm with a little bit of 1.2.
a long continuous weld builds up a huge amount of heat
whats your helmet like if its set to dark then you will be having issues of not seeing the heat properly.
but
dont have it set to light either as arc eye is a bitch
also try spot migging on the panel steel, with a slighty hotter setting, start on the weld and pull the pool across onto the sheet, then off and start again starting back on the weld just done, ive found that this works quite well and im using 1.0 wire onto LC panels which would be 1.0-1.2 at a guess
i would be using around 25%-30% on a 250amp unit and getting reasonably flat welds with full penetration.
the donner steel is mainly 1.6mm with a little bit of 1.2.
a long continuous weld builds up a huge amount of heat
Re: Help Needed Apply Within...
waza4x4toy wrote:Hi should try welding a jeep the panel steel is not like the cans your jappa is made of Caleb may be that's the problem![]()
![]()
![]()
check out this nz you tuber he has about a dozen great panel and welding clips
See this one on welding panel [url]http://m.youtube.com/watch?v=zdsOGDzuIps&desktop_uri=%2Fwatch%3Fv%3DzdsOGDzuIps/url]
Very helpful and useful tips and tricks on most panel work.... his youtube ID is "restolad" if the above link is not working
Cheers W
Your just jealous that you cant drive around in your old beer cans



027 MUD GEAR - (027 683 4327)
Check our facebook:
http://www.facebook.com/Filthy4x4
http://www.facebook.com/Filthymotorsportnz
Re: Help Needed Apply Within...
mudlva wrote:just thought of something
whats your helmet like if its set to dark then you will be having issues of not seeing the heat properly.
but
dont have it set to light either as arc eye is a bitch
also try spot migging on the panel steel, with a slighty hotter setting, start on the weld and pull the pool across onto the sheet, then off and start again starting back on the weld just done, ive found that this works quite well and im using 1.0 wire onto LC panels which would be 1.0-1.2 at a guess
i would be using around 25%-30% on a 250amp unit and getting reasonably flat welds with full penetration.
the donner steel is mainly 1.6mm with a little bit of 1.2.
a long continuous weld builds up a huge amount of heat
I think ive got the helmet adjusted to a comfortable setting at least, may give it a tune up tomorrow to see if it helps.
I started off doing spot welds then the second time around I tried doing about 20mm welds, the third time I had the heat up on 40amps with about 15.2volts and quite a fast wire speed to try reduce the undercutting but it turned out the worst of the lot



Does it need to be fully welded to perfection or is there a magic "seam sealer" type product that I can put on to fill the gaps and make it water tight?
Cheers

027 MUD GEAR - (027 683 4327)
Check our facebook:
http://www.facebook.com/Filthy4x4
http://www.facebook.com/Filthymotorsportnz
- mudlva
- Hard Yaka
- Posts: 2918
- Joined: Mon Apr 16, 2007 12:00 pm
- Location: fixing another cv!! dam lockers (Papakura)
Re: Help Needed Apply Within...
are you pushing the weld pool or pulling it?
i pull the weld when on sheet metal as it tends to have a better reaction on keeping the weld thickness up verse pushing the weld, it is also easier to push the wire straight through the sheet creating big arse holes
panel hitters use a product called urethane to stick, seal glue every thing together with, a bit like a builder running around with a tube of salleys all clear silicon at a guess
i pull the weld when on sheet metal as it tends to have a better reaction on keeping the weld thickness up verse pushing the weld, it is also easier to push the wire straight through the sheet creating big arse holes

panel hitters use a product called urethane to stick, seal glue every thing together with, a bit like a builder running around with a tube of salleys all clear silicon at a guess
Re: Help Needed Apply Within...
mudlva wrote:panel hitters use a product called urethane to stick, seal glue every thing together with, a bit like a builder running around with a tube of salleys all clear silicon at a guess
Ya cheeky bugger..


Re: Help Needed Apply Within...
mudlva wrote:are you pushing the weld pool or pulling it?
i pull the weld when on sheet metal as it tends to have a better reaction on keeping the weld thickness up verse pushing the weld, it is also easier to push the wire straight through the sheet creating big arse holes![]()
panel hitters use a product called urethane to stick, seal glue every thing together with, a bit like a builder running around with a tube of salleys all clear silicon at a guess
Pulling the weld seemed alot easier to me. Have created and filled some good holes

So there isnt a magic bog that will actually fill and make water tight?
Maybe I should just mask and urethane a strip down the middle



027 MUD GEAR - (027 683 4327)
Check our facebook:
http://www.facebook.com/Filthy4x4
http://www.facebook.com/Filthymotorsportnz
Re: Help Needed Apply Within...
Big wrote:mudlva wrote:panel hitters use a product called urethane to stick, seal glue every thing together with, a bit like a builder running around with a tube of salleys all clear silicon at a guess
Ya cheeky bugger..Not all builders are like that..
I spot weld with C02( apparently give better penetration than argsheild) 180 amp job ,if your mig is a goodie.. You just have to be fast with the trigger, it'll get good penetration won't warp as much BUT it does take a while as you spot in different areas to keep the steel cool OR you can use a air gun and blow cool air onto the steel straight away After you have spot welded it and it'll take the heat out of it.. bit like the copper thing before I suspect.. works ok but it does take a bit.. I guess you can use a lot of techniques as there are a lot of ways to achieve the same result.. practise makes perfect.. good luck
I asked one of the guys that sells the gas and he said that you cant use c02 for doing panel steel, more good advice from someone who loves his job

I will try find some copper to try it with, have thought about air but wasnt sure if it would be sufficient.
I just dont want to completely destroy it, im sure its getting worse by trying to make it better



027 MUD GEAR - (027 683 4327)
Check our facebook:
http://www.facebook.com/Filthy4x4
http://www.facebook.com/Filthymotorsportnz
Re: Help Needed Apply Within...
I'd say a sales pitch to get you to buy arg shield.. it's more expensive.. I use c02 as it's cheap , don't need an acc and easy to get filled or swap..
Im going to have a play over the next week or so as doing repairs etc.. mods so will try to see what it does to make sure .. I think main thing with migs is cleanliness is godliness when zipping up steel.. if there is any dirt, paint, anything then it'll splatter and you get unsatisfactory welds..lol to say the least..
Im going to have a play over the next week or so as doing repairs etc.. mods so will try to see what it does to make sure .. I think main thing with migs is cleanliness is godliness when zipping up steel.. if there is any dirt, paint, anything then it'll splatter and you get unsatisfactory welds..lol to say the least..

Re: Help Needed Apply Within...
Yeah could have been, i didnt end up buying off them anyway they wanted way too much
I might have another play around with a few things and see how I get on.
If anyone wants to come cast an eye over it I wont stop ya


I might have another play around with a few things and see how I get on.
If anyone wants to come cast an eye over it I wont stop ya



027 MUD GEAR - (027 683 4327)
Check our facebook:
http://www.facebook.com/Filthy4x4
http://www.facebook.com/Filthymotorsportnz
Re: Help Needed Apply Within...
Big wrote: I spot weld with C02 (apparently give better penetration than argsheild)
My understanding is the opposite way around bro. They put the argon in Argoshield to help stabilize the arc and give better penetration (specifically at lower amp settings, in mild steel)
The combo of argon/carbon dioxide will penetrate mild steel better than either gas alone.
Caleb,
BOC do a gas called "argosheild light" which is specifically for panel steel (less penietration than normal argoshield) which may make your life easier (I have never tried it so can't say).
Definitely stick to your .6mm wire . Just cause its easier in so much as you can use lower settings on your welder, so can do a bit more of a run before getting too much heat in the work piece and blowing through/warping.
I have had success using the spot weld technique Mudlva was saying about. It can give quite a tidy result and works well for the more tricky bits. Also definitely "pull" the gun rather than "pushing" it for panel steel. Other wise you just blow through as soon as you get a good bead going.
If it is undercutting badly double check your gas. I once had a situation where BOC mistakenly supplied me with straight argon when I swapped my argoshield bottle (and still invoiced me for argosheild). Over night my welding turned to shit and I didn't know why. Panel welds were pokey, never setting up a good arc. 4 & 5mm steel welds were proud and lacked penetration. The mistake was only picked up when I went to exchange the bottle again and they tried to give me Argon (as per the bottle I returned). The advice from BOC's guru on the end of the phone was grind out every single structural weld and re do it.
Sorry if I just told you how to suck eggs.
Also note that the only qualification I have to justify my advice is the experience from panel work I have done on my own projects.
Re: Help Needed Apply Within...
Cheers, I shall do a bit more practice and see how I end up, I might start in a new area today
What sort of amps, volts do you guys use?
I suppose I should have also said im using 0.8 panel.

What sort of amps, volts do you guys use?
I suppose I should have also said im using 0.8 panel.

027 MUD GEAR - (027 683 4327)
Check our facebook:
http://www.facebook.com/Filthy4x4
http://www.facebook.com/Filthymotorsportnz
- mudlva
- Hard Yaka
- Posts: 2918
- Joined: Mon Apr 16, 2007 12:00 pm
- Location: fixing another cv!! dam lockers (Papakura)
Re: Help Needed Apply Within...
from what ive read and been told is that co is good with the heavy weld but it will splatter lots more then mixed gas
with 0.6 wire onto 0.8 s/m and using a 175 machine then i would be starting at around 30/40% dropping down to get the flow with the spotting technique.
also you need just enough gas to weld with it should not be blowing out.
with setting the gas start with none and adjust upwards until the weld starts to form as it should then wind it back down until it starts to look and sound like crap, then just a touch more flow, now this is your std start position, if it starts to go bubbly then a touch more again. to much gas and it will affect the weld and you are just wasting money
with 0.6 wire onto 0.8 s/m and using a 175 machine then i would be starting at around 30/40% dropping down to get the flow with the spotting technique.
also you need just enough gas to weld with it should not be blowing out.
with setting the gas start with none and adjust upwards until the weld starts to form as it should then wind it back down until it starts to look and sound like crap, then just a touch more flow, now this is your std start position, if it starts to go bubbly then a touch more again. to much gas and it will affect the weld and you are just wasting money
Re: Help Needed Apply Within...
well shit, I guess you learn something everyday.. Might try it..
Always looking at making welding easier..lol

Re: Help Needed Apply Within...

stick with on off welding or stack the dot, this will allow you to weld easier, the technique has been discribed above, will give you a nice tidy weld
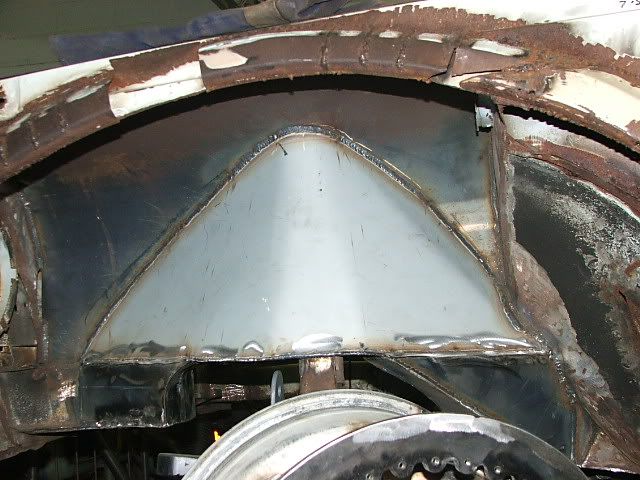
A little tip that will help if you can manage put a fold in the panel so that you double back the edge, so your welding corner to corner, this is a good trick when welding across big panels as it adds a structure that will resist warp or overlap the edges by a mm or two, this will give you a bit more material in the weld to soak up the heat
before you start to weld you want spot welds along the join about an inch apart, this will help control the warpage and keep your material pulling apart
Re: Help Needed Apply Within...





Will be asking Santa for a miracle and a new reg and bottle



027 MUD GEAR - (027 683 4327)
Check our facebook:
http://www.facebook.com/Filthy4x4
http://www.facebook.com/Filthymotorsportnz
Re: Help Needed Apply Within...
lol welcome to engineering.... I can nail a D size on the tig in a couple of days
Welding inside on panel using the tac weld technique I'll wind the gas flow down to 5-6L, your post and pre flow will give you enough to shield, please note if you try and pull a bead at this flow level the heat from the weld will move the shield gas away from the weld
If your renting a bottle its cheaper per volume to refull a larger bottle
Welding inside on panel using the tac weld technique I'll wind the gas flow down to 5-6L, your post and pre flow will give you enough to shield, please note if you try and pull a bead at this flow level the heat from the weld will move the shield gas away from the weld
If your renting a bottle its cheaper per volume to refull a larger bottle

Re: Help Needed Apply Within...
I found outside welding is easy enough with gasless wire,
cringe all you like but when its a bit windy it works.
also positioning of the torch and the wires feed point into the pool had a great effect on my welding,
biggest thing to remember is heat rises,
you get a pool of molten steel and the heat will transfer to the top of that pool, if you putting the wire up there also it creates more heat which if you are moving the pool slowly will blow through.
horizontal stroke on panel steel I find the hardest ,
downstroke the easiest and upstroke I stack the spots.
if your panels have a little gap between them try a lower amperage and wirespeed so you can generate a pool then wave the torch to catch both pieces of steel with out generating to much heat whilst you drag it along the butt
cringe all you like but when its a bit windy it works.
also positioning of the torch and the wires feed point into the pool had a great effect on my welding,
biggest thing to remember is heat rises,
you get a pool of molten steel and the heat will transfer to the top of that pool, if you putting the wire up there also it creates more heat which if you are moving the pool slowly will blow through.
horizontal stroke on panel steel I find the hardest ,
downstroke the easiest and upstroke I stack the spots.
if your panels have a little gap between them try a lower amperage and wirespeed so you can generate a pool then wave the torch to catch both pieces of steel with out generating to much heat whilst you drag it along the butt
problems are only a problem if you not willing to learn how to find solutions
Re: Help Needed Apply Within...
Filthy4x4 wrote:mudlva wrote:are you pushing the weld pool or pulling it?
i pull the weld when on sheet metal as it tends to have a better reaction on keeping the weld thickness up verse pushing the weld, it is also easier to push the wire straight through the sheet creating big arse holes![]()
panel hitters use a product called urethane to stick, seal glue every thing together with, a bit like a builder running around with a tube of salleys all clear silicon at a guess
Pulling the weld seemed alot easier to me. Have created and filled some good holes![]()
So there isnt a magic bog that will actually fill and make water tight?
Maybe I should just mask and urethane a strip down the middle![]()
Hi Filthy,
Hold fast, Carbond 940 FC
http://www.holdfast.co.nz/pages/product ... psid=20054
OR
Wurth, KD Bond + Seal
We use both at work to seal/ Glue panels to truck bodies etc.
Same stuff you seal smeared all through the seams of your jappa engine bay / boot.
Re: Help Needed Apply Within...
CO2 does give better penetration but when welding thin sheet over-penetration is usually the issue not under-penetration. Argoshield light is the gas you want for thin sheet.
At the end of the day welding thin sheet steel like that used for vehicle body panels is a skill that only comes with practice. Even very experienced welders sometimes embarrass themselves terribly when faced with an apparently simple rust job on a car.
A tip - When prepping the metal for welding use a DA sander not a sanding disc on an angle grinder as it removes too much material and there is no spare material thickness on vehicle body panels.
There's a number of tricks you can use such as:backing up the weld with a copper backing block (if you can access the rear of the weld), pulse welding etc. I'd recommend you have a look at some of the instructional videos on Youtube until you see something that looks like it will work in your application.
Good luck.
BTW - I don't work for BOC. I have no shares in the company that sells Argoshield. I've spent a bit of time asking people why they use expensive Argoshield on big jobs when CO2 will do the job better and cheaper, but for the thin stuff CO2 just doesn't cut it.
At the end of the day welding thin sheet steel like that used for vehicle body panels is a skill that only comes with practice. Even very experienced welders sometimes embarrass themselves terribly when faced with an apparently simple rust job on a car.
A tip - When prepping the metal for welding use a DA sander not a sanding disc on an angle grinder as it removes too much material and there is no spare material thickness on vehicle body panels.
There's a number of tricks you can use such as:backing up the weld with a copper backing block (if you can access the rear of the weld), pulse welding etc. I'd recommend you have a look at some of the instructional videos on Youtube until you see something that looks like it will work in your application.
Good luck.
BTW - I don't work for BOC. I have no shares in the company that sells Argoshield. I've spent a bit of time asking people why they use expensive Argoshield on big jobs when CO2 will do the job better and cheaper, but for the thin stuff CO2 just doesn't cut it.
Re: Help Needed Apply Within...
Thanks guys
I actually have some carbond floating around, im trying to weld as much as I can so I dont have to bog much
well thats how the theory goes anyway...
Im slowly getting the hang of it.... I think. New reg and argoshield light made a big difference.





I actually have some carbond floating around, im trying to weld as much as I can so I dont have to bog much


Im slowly getting the hang of it.... I think. New reg and argoshield light made a big difference.





027 MUD GEAR - (027 683 4327)
Check our facebook:
http://www.facebook.com/Filthy4x4
http://www.facebook.com/Filthymotorsportnz
-
- Driver/Navigator
- Posts: 15
- Joined: Wed Jan 22, 2014 7:54 pm
- Location: Hibiscus coast
Re: Help Needed Apply Within...
G'day, I didn't read the last few posts as it looks like things are going ok. I live in red beach if you still want a hand ( panel beater 14 years )but thought I would mention 3m bonding adhesive with reading about sealing up areas etc. basically it's a glue that sticks like $h!t to anything. It's used to glue new panels together, or on, eliminating welding. I have glued a new roof onto a lwb high roof transit van with 1 x weld in the four corners, fully approved by collision repair association etc. I have also used it to stick a stainless sender bracket onto a tinny, dragged it up the beach many times and was worried that it was going to tear a hole in the transom! As long as the prep work is done right it's magic stuff. Even if you tack on a patch etc the glue can be used to seal over it, sanded then filler used over the top. I plan to cut sum rust from the roof of my sj413, glue patches from behind then fill from the outside. No burns, no distortion etc.
My biggest fear is if I die my wife will sell my toys for what I told her they cost!
Re: Help Needed Apply Within...
Old school wrote:G'day, I didn't read the last few posts as it looks like things are going ok. I live in red beach if you still want a hand ( panel beater 14 years )but thought I would mention 3m bonding adhesive with reading about sealing up areas etc. basically it's a glue that sticks like $h!t to anything. It's used to glue new panels together, or on, eliminating welding. I have glued a new roof onto a lwb high roof transit van with 1 x weld in the four corners, fully approved by collision repair association etc. I have also used it to stick a stainless sender bracket onto a tinny, dragged it up the beach many times and was worried that it was going to tear a hole in the transom! As long as the prep work is done right it's magic stuff. Even if you tack on a patch etc the glue can be used to seal over it, sanded then filler used over the top. I plan to cut sum rust from the roof of my sj413, glue patches from behind then fill from the outside. No burns, no distortion etc.
Is this the stuff?
http://3mcollision.com/3m-panel-bonding-adhesive-08115.html
-
- Driver/Navigator
- Posts: 15
- Joined: Wed Jan 22, 2014 7:54 pm
- Location: Hibiscus coast
Re: Help Needed Apply Within...
Yep, if your going to use it you need to watch some vids on you tube etc. done right it's fantastic stuff.
My biggest fear is if I die my wife will sell my toys for what I told her they cost!